Constructor Awards
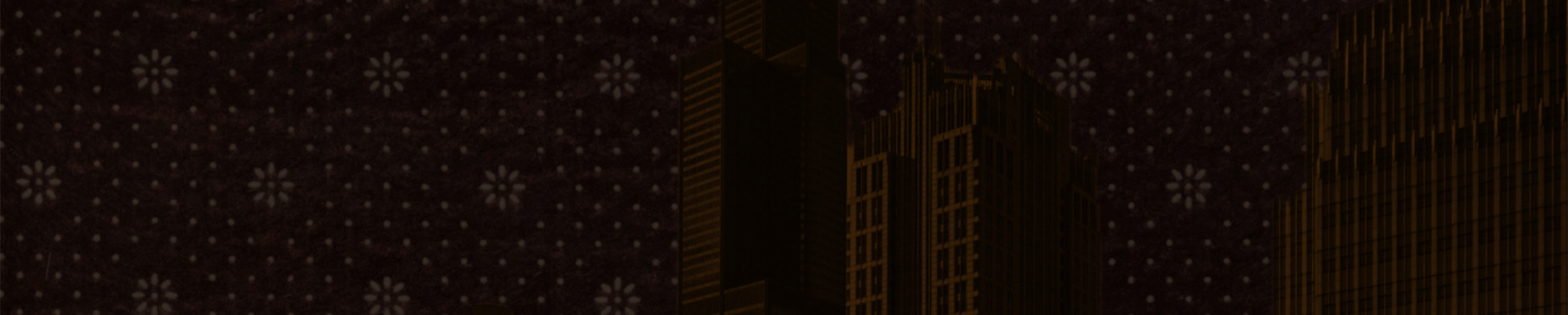
Celebrating the Best in California’s Construction Industry
It’s not the magnitude of a building or breadth of a bridge that makes California’s construction industry great; it’s the groundbreakers and trailblazers at the forefront of these achievements who have built a legacy in California’s construction industry. AGC of California’s Constructor Awards honor the teams who lead the industry through innovation.
2025 CONSTRUCTOR AWARD FINALISTS
SPECIALTY $10 MILLION & UNDER
ISEC, Inc.– Mission Rock
The Mission Rock project, part of the China Basin Park at 1051 3rd Street, San Francisco, CA, was completed on January 18, 2024, with a project value of $1.44 million. ISEC was responsible for constructing the utility fence, Stormwater Boardwalk, overlook deck, and wood slat seating. This marked ISEC’s first foray into exterior projects, showcasing their adaptability and problem-solving prowess. The project’s success hinged on effective management and coordination, particularly in vendor selection, which resulted in cost and time efficiencies. Vendors were carefully chosen for their cost-effectiveness and time efficiency, ensuring alignment with project goals and timelines.
The team faced scheduling challenges due to unexpected rain, which required swift adjustments to minimize impacts. Safety was paramount, especially on the overlook deck, where significant fall hazards existed. ISEC mandated that all installers use appropriate fall protection equipment when working at elevated heights, coupled with comprehensive training sessions to ensure equipment safety and address potential issues. The structural steel level work on the Stormwater Boardwalk was challenging due to shifting terrain, necessitating the use of stable, secure elevated platforms instead of ladders. Thorough terrain assessments and modifications were conducted to create a safer working environment. The Mission Rock project exemplifies ISEC’s commitment to safety, efficiency, and effective teamwork in new construction settings.
Royal Electric Company– UC Davis Health Shared Services Center Project
Located in Sacramento, CA, the UC Davis Health Shared Services Center project exemplifies Royal Electric Company’s commitment to overcoming challenges and promoting career growth. Completed on January 18, 2024, this 92,000 SF state-of-the-art facility functions as a pharmacy fulfillment center, transforming pharmaceutical distribution for both inpatient and outpatient care. This project was a collaborative endeavor with Jackson Properties, Jackson Construction, and UC Davis Health.
Initially delayed by 11 months due to lease negotiations, the project faced challenges such as extended equipment lead times. Royal Electric responded with innovative prefabrication techniques, designing and installing critical systems like medium voltage utility infrastructure and an emergency power system with a 1.25-megawatt generator. The facility features advanced equipment, including a conveyor belt system and clean rooms, necessitating precise execution and coordination.
The project’s success hinged on Royal Electric’s ability to implement lean principles, preplanning, and strategic collaboration with stakeholders. The use of AI technology, OpenSpace, ensured accurate documentation and minimized costly change orders. Royal Electric’s leadership and proactive problem-solving enabled the project to meet aggressive deadlines, achieving a timely certificate of occupancy.
SPECIALTY $10 MILLION & OVER
Royal Electric Company – Taxiway D&T Reconstruction Project
The Taxiway “Delta” & “Tango” Reconstruction Phase 2 project at San Francisco International Airport (SFO) aimed to realign taxiways to enhance aircraft safety and efficiency, addressing FAA-identified blind spots. Royal Electric, subcontracted by Golden Gate Constructors, was pivotal in updating airfield lighting by installing 525 base cans, 375 light fixtures, and over 26,000 feet of conduit, alongside constructing duct banks and a new fuel vault electrical system.
Beginning in January 2024, the project faced three months of extreme wet weather, causing significant delays and scope expansion. Despite these challenges, an acceleration plan was implemented, allowing completion three weeks ahead of schedule by working around the clock in the final weeks. The project scope involved precision demolition, careful handling of buried sectional pull boxes, and intricate coordination for a planned Terminal E shutdown, all without compromising quality or safety.
Key achievements included a 575-foot bore shot for conduits, establishing a new duct bank, and installing critical infrastructure for the FAA control tower. The construction of the fuel vault required specialized materials and extensive coordination with multiple stakeholders, showcasing Royal’s adept project management and resourcefulness.
HEAVY CIVIL $10 MILLION & UNDER
Hal Hays Construction, Inc. – Electric Vehicle Infrastructure Improvements – Prologis (Denker) “Denker Project”
Denker Infrastructure’s Denker Hub project, located on Denker Avenue in Los Angeles, is strategically positioned to support the Ports of Los Angeles and Long Beach, which are crucial for U.S. imports and exports. The project was accelerated through partnerships with the Los Angeles Department of Water and Power, the City of Los Angeles, and Southern California Gas. These collaborations facilitated the development of a 9 MW charging microgrid at the nation’s largest heavy-duty EV truck charging depot, powered by hydrogen-ready Mainspring Linear Generators. This microgrid supports 96 EV ports, charging over 300 trucks daily, significantly reducing emissions compared to traditional diesel fleets.
Denker Infrastructure integrated advanced technologies, including 24 DC power cabinets, 96 EVSE ports, and 12 Linear Generator Units. The project achieved a milestone by completing Node 1 of 6 in just five months, despite challenging weather conditions. Key features include a self-contained microgrid, 18 MW of energy storage, and a design that accommodates various renewable fuels, showcasing a forward-thinking approach to transportation electrification. The project serves as a prototype for future EV infrastructure and contributes to reducing greenhouse gas emissions, aligning with broader environmental goals.
Myers & Sons Construction – Del Valle Dam – Bulkhead Installation and Spillway Repair Project
Del Valle Dam project encompassed essential refurbishment tasks, including inspection and repair of a bulkhead gate for the California Department of Water Resources. Key activities involved replacing rubber seals, hydraulic lines, and valves, using underwater services for bulkhead installation and removal, tunnel dewatering, and installing new gate systems. Additional efforts included fabricating metal walkways, ladders, and constructing a storage setup with concrete pads. Unknown project scope posed a challenge, necessitating preliminary work to gauge further requirements. A tight procurement timeline for the slide gate was efficiently handled by Myers & Sons Construction, leveraging vendor relationships and clear communication. Adherence to Tunnel Safety Orders ensured safety, with continuous air monitoring and an on-site rescue team. Personnel were trained and equipped with M65 MSHA rescue breathers. Despite challenges like a shortened work window due to fluctuating lake levels, the project concluded in weeks rather than months. Through effective contingency planning and self-performance capability, Myers & Sons Construction delivered the project on schedule, meeting DWR’s expectations.
HEAVY CIVIL $10 MILLION TO $25 MILLION
CalPortland Construction – Gaviota Secant Wall Emergency Project
In response to severe flooding and erosion threatening the structural integrity of US Highway 101 along Gaviota Creek in Santa Barbara County, the Secant Wall Emergency Project was initiated. CalPortland Construction was contracted under an emergency agreement to address the compromised sections, with the project running from June 2023 to April 2024 at a cost of $14.5 million. This effort involved designing a secant wall using 1000mm CIDH piles, reinforced with W24x250 beams, to stabilize the creek banks and prevent further collapse. The construction required a temporary creek diversion and implemented a single-lane detour for southbound traffic.
Design alternatives considered included the placement of the secant wall either adjacent to or directly beneath the highway barrier. The final design aligned the wall with existing structures, incorporating a pile cap and type 842 barrier. Key subcontractors, such as Malcolm Drilling and Vista Steel, were engaged for pile installation and reinforcement.
Construction methods addressed access challenges in unstable conditions by using a temporary shale embankment. The drilling process was phased to prevent hole collapse, with temporary casing and drilling fluid employed for stability. Coordination with Caltrans was crucial, as the project overlapped with the ongoing Nojoqui Project, requiring flexible scheduling and sequencing to minimize disruptions.
Environmental compliance was a priority, involving coordination with multiple agencies and implementing a dewatering and diversion plan to protect local ecosystems. Full-time biological monitoring ensured species protection, and environmental awareness training was conducted for all personnel.
Granite Construction Company – Santa Claus Lane Bike Path
The Highway 101 Santa Claus Lane Bike Path offers a vital connection from Santa Claus Lane in Santa Barbara County to Carpinteria, enhancing bicycle and pedestrian travel alongside Highway 101. The project involved constructing gravity walls, a sheet pile wall, storm drain improvements, and safety barriers, including a Type 85 concrete barrier rail and tube and cable railings. Recognized as the 2024 Active Transportation Project of the Year by the California Transportation Foundation, the path significantly improves access between local beaches and Carpinteria Avenue.
Granite’s partnership with Caltrans, using CMGC processes, facilitated effective risk management and stakeholder alignment, leading to substantial savings and improved functionality. Coordination with Union Pacific Railroad ensured timely installation of the sheet pile wall, while collaboration with SoCalGas maintained safety around a high-pressure gas line. Early scheduling and strategic planning minimized disruptions to local businesses and environmental impacts, with winterization plans allowing work to proceed smoothly during wet seasons.
Innovative solutions, such as substituting gravity walls for sheet piles, contributed to approximately $950,000 in savings. Granite’s preconstruction reviews further identified redundant drainage elements, saving $125,000. The use of a Giken Silent Piler instead of traditional methods for sheet installation demonstrated problem-solving excellence, ensuring safety and efficiency.
Skanska USA Civil – I-15 Median Fill Various Locations from Harvard Road Overcrossing to Rasor Road Overcrossing
Aiming to improve traffic flow between Los Angeles and Las Vegas, the I-15 Widening Project focused on alleviating congestion along a 35-mile stretch between Victorville and Barstow. This initiative included safety enhancements on State Highway I-15 in San Bernardino, with construction extending from just south of Harvard Road to north of Rasor Road. The project involved comprehensive reconstruction of roadways, ramps, bridges, and drainage facilities, along with resurfacing existing highways. Key improvements featured the widening of four bridges, reconstruction of a structural steel railroad over-crossing, and the addition of 13 retaining walls, complemented by drainage upgrades. These enhancements significantly improved traffic flow and safety along this busy highway corridor.
A major challenge was maintaining open lanes during peak hours as required by Caltrans, which necessitated night and split-shift operations. To facilitate this, Skanska constructed two temporary median lanes, allowing for the uninterrupted widening of permanent lanes. The project faced extreme climate conditions, with summer temperatures reaching 120 degrees and winter temperatures falling below freezing. Skanska utilized its aggregate-producing resources, including portable crushing and asphalt plants, for material processing. These strategic innovations and considerations enabled the project’s early completion and improved safety conditions for the construction team.
Teichert Construction – Hallwood Side Channel & Floodplain Restoration
The Hallwood Side Channel & Floodplain Restoration project aimed to restore ecological processes and enhance flood resilience in Marysville, focusing on 150 acres of riparian floodplain and multiple side channels. This initiative, a public-private partnership, highlighted the collaboration between diverse stakeholders including environmental organizations, government agencies, and construction firms. The project faced challenges such as managing multiple stakeholders, coordinating construction schedules around river conditions, and navigating flood season restrictions.
Innovative solutions were crucial, such as employing a Bailey Bridge for efficient access to work areas, and utilizing onsite conveyor systems to reduce transportation costs. The project emphasized using environmentally friendly materials, including native vegetation and eco-friendly oils in construction equipment, to minimize ecological impact. Over 25,000 native plants were strategically planted to ensure habitat sustainability, while hardwood from nearby sources was repurposed for habitat creation.
Despite challenges, the project was completed on time and within budget, with significant contributions from Teichert valued at approximately $90 million. The restoration efforts have already shown positive results, with increased salmon and steelhead habitat usage. The project has improved flood resilience by removing 3.2 million cubic yards of sediment, reducing flood risks for local communities, and reversing ecological impacts from historic gold mining.
HEAVY CIVIL $25 MILLION TO $50 MILLION
Granite Construction Company – BNSF Needles Third Main Track Project
The BNSF Needles Third Main Track Project involved constructing a 29-mile third rail line parallel to an existing track in a challenging desert environment. This complex endeavor required extensive excavation, including 340,000 cubic yards of dirt and 30,000 cubic yards of granite rock, and the placement of 97,000 cubic yards of subballast. The project also included extending 48 culverts, driving 651 steel piles, and building 50 new bridges and crash protection walls under Interstate 40. Working in a sensitive environmental area, the team implemented a robust Environmental Compliance Plan to mitigate impacts, particularly to protect species like the Desert Tortoise.
Originally planned as a bid-build, the project shifted to a CM/GC Lite approach, allowing for enhanced collaboration among BNSF, Granite, and other stakeholders. This shift enabled early constructability reviews and risk assessments, leading to cost savings and scheduling efficiencies. Site access and staging were improved through strategic planning and environmental considerations, facilitating project logistics without ecological disruption.
Managing train operations along the Southern Transcon, the busiest BNSF corridor, required precise coordination to avoid service disruptions. Despite challenges such as remote location and adverse weather conditions, the project maintained an impressive safety record with over 82,000 man-hours worked without OSHA recordables. Early material procurement and innovative solutions, including drilling a new well for construction water, contributed to the project finishing on time and under budget. Recognized for its excellence, the project won several awards, including the California Transportation Foundation’s Goods Movement Project of the Year 2024.
Griffith Company – SR-57-60 Confluence Chokepoint Relief Program (Phase 1) The Diamond Bar Golf Course Project
As part of the Diamond Bar Golf Course renovation, the Diamond Bar Creek project navigated significant environmental and operational challenges, including adherence to a Streambed Alteration Agreement in line with California Department of Fish and Wildlife regulations. Faced with extreme weather conditions in 2022 and 2023, such as rare atmospheric river storms and Tropical Storm Hilary, the Griffith Company led the initiative with effective water diversion strategies. By employing dewatering, gravel bags, and robust BMPs, the project successfully controlled erosion and sediment, safeguarding environmentally sensitive areas.
The project emphasized sustainable practices by reducing turf areas by over 33 acres, saving 28 million gallons of water annually, cutting future maintenance costs, and reducing emissions. These efforts were supported by innovative irrigation adjustments and the use of alternative ground covers. Safety was a top priority, with 154,000 man-hours completed without lost-time incidents, achieved through proactive safety measures and rigorous inspections.
The project, completed on time and within its $50 million budget, improved stream facilities, reduced water usage, and enhanced environmental sustainability. It recycled 100% of hard removals and incorporated weathering steel and bioswales to improve durability and stormwater management. More than 1,000 plants and trees were added to promote ecological health.
Myers & Sons Construction – Lytton Rancheria On-Site Water Treatment Plant and Wastewater Treatment Plant
Myers & Sons Construction was chosen by the Lytton Band of Pomo Indians for the design-build of new water and wastewater treatment plants at Lytton Rancheria in Windsor, California. This project is part of broader site development plans including 147 homes, a community center, and retreat center. Engaging Myers early allowed for input in the site plan, ensuring the infrastructure supports future expansion. Through collaboration, both plants were designed to accommodate long-term needs without expanding their physical footprint, simply activating new sections as required.
Challenges included designing a Title 22 Recycled Water system sensitive to the nearby Russian River, building in a high wildfire area, and ensuring the infrastructure blended with the natural landscape. Myers also navigated working with other contractors, PG&E delays, and addressing concerns from the City of Windsor. The collaborative and iterative approach enabled the evaluation of various infrastructure options suited to the evolving project plans. Successfully completed in under three years, the project exemplified effective design-build collaboration, with both the Lytton Tribe and Myers committed to delivering a sustainable and efficient infrastructure solution.
Skanska USA Civil – SR-60 Moreno Beach Dr Intersection, Phase 2
The SR-60/Moreno Beach Drive project in Moreno Valley, CA, involved replacing a two-lane bridge with a six-through lane bridge and reconfiguring the SR-60/Moreno Beach Interchange along with a westbound auxiliary lane. Initially left at 15% completion, the City of Moreno Valley appointed Skanska to advance the project. Upon agreement finalization, Skanska promptly mobilized to meet the tight completion schedule. The team introduced modifications to the staging plans, enhancing vehicle capacity through the ongoing project, thus easing traffic congestion.
Safety and environmental integrity were priorities; Skanska implemented additional measures, including k-rail and positive protection, improving safety for freeway traffic within the work zone. To maintain traffic flow, two major closure windows were executed timely to shift traffic onto new stages of Moreno Beach Drive, minimizing disruptions. Skanska adeptly managed the procurement of long lead equipment, such as electrical transformers, by collaborating with utility agencies and subcontractors, ensuring adherence to the aggressive timeline. The project was completed 11 days ahead of schedule, without any safety incidents, showcasing Skanska’s effective project management and innovative solutions, meeting the City’s expectations and significantly improving infrastructure in the area.
HEAVY CIVIL $50 MILLION TO $150 MILLION
Granite Construction Company – Highway 101 Segment 4C
The Highway 101 Segment 4C Project significantly enhanced a key corridor connecting Ventura and Santa Barbara by reconstructing 2.6 miles of highway to include three lanes in each direction and two HOV lanes. The project involved major infrastructure upgrades, including rebuilding two interchanges, constructing new bridges, and implementing extensive drainage and retaining wall systems. Over 38,000 tons of HMA and 37,000 cubic yards of CRCP were used, with Granite self-performing 80% of the work.
Granite collaborated closely with Caltrans to ensure successful delivery. This partnership facilitated effective communication and problem-solving, resulting in zero delays, claims, or litigation. The project addressed challenges such as nesting Cormorants, which were mitigated through collaborative environmental planning. Critical issues like a design flaw in Soundwall 102 were resolved efficiently, maintaining the project timeline.
Manson Construction, Co. – P-443 Pier 6 Replacement at Naval Base San Diego
Executed by Manson Construction for NAVFAC Southwest, the P-443 Pier 6 Replacement project at Naval Base San Diego marked a significant achievement. This Design-Build initiative replaced an outdated pier from 1945 with a modern, single-deck berthing pier, boosting the base’s operational capabilities. Previously, the 1,377 ft by 60 ft structure struggled to meet the demands of the Navy’s growing fleet due to obsolete utilities. The newly constructed pier, spanning 1,500 ft by 120 ft, features 516 prestressed concrete piles and over 17,000 cubic yards of cast-in-place concrete, allowing it to accommodate four contemporary naval vessels with upgraded utilities and appurtenances.
Innovative planning and collaboration with WSP USA allowed for simultaneous demolition and reconstruction, minimizing disruption to base operations. The project was completed a month ahead of schedule, with key milestones like pile driving and concrete pours finished early. A strong partnership between Manson Construction and NAVFAC Southwest ensured no major rework or claims, maintaining excellent communication and safety standards throughout. Manson Construction received outstanding evaluations in CPAR, with ratings indicating exceptional quality, management, and regulatory compliance, reflecting the project’s success and efficient execution within a secure, operational environment.
Teichert Construction – Veterans Boulevard Interchange
The Veterans Boulevard Interchange Project is a transformative infrastructure development connecting Fresno’s “forgotten part” to State Route 99 (SR-99), enhancing traffic flow and accessibility. This historic undertaking, the largest public works project in Fresno’s history, was completed by Teichert and MCM on time and on budget. It involves constructing a six-lane super-arterial roadway, a freeway interchange, multiple bridges, new ramps, and a grade-separated pedestrian and bicycle trail. The project honors veterans and employed many in its construction.
Effective management and innovative solutions were pivotal. Teichert implemented value engineering, saving over $1 million, and revised the traffic detour plan to keep freeway traffic off local streets, reducing congestion and improving safety. The project included complex coordination with concurrent Caltrans, City of Fresno, and High-Speed Rail projects, ensuring seamless integration and minimizing public disruption.
Bogh Engineering, LLC – Enhanced Recharge Phase 1B Project
The Enhance Recharge Project Santa Ana River Basins Phase B1 (ERP) is a significant initiative by the San Bernardino Valley Municipal Water District (SBVMWD) and Bogh Engineering, aimed at securing the water future for over a million residents from Redlands to Corona. This 600-acre project is a part of a long-term strategy to ensure the reliability and resilience of the local groundwater aquifer by diverting water from the Seven Oaks Dam and the State Water Project into newly constructed basins for aquifer recharge. Successfully completed 12 months ahead of schedule and under budget by $5 million, the project showcases exemplary leadership and collaboration between SBVMWD and Bogh.
Innovative construction techniques, such as repurposing native materials for basin construction and on-site precast concrete wall production, expedited completion and reduced costs. The basins began capturing water 18 months ahead of schedule, amassing 80,000 acre-feet during construction, vastly exceeding previous records. The project’s infrastructure, including a mile-long channel and 56 precast structures, allows precise water flow control, supported by solar panel-operated stilling wells for remote data collection.
ERP’s environmental emphasis included safeguarding endangered species like the Kangaroo Rat, with half the site dedicated to conservation efforts. This partnership between environmentalists and contractors ensured minimal ecological disruption while progressing ahead of schedule. ERP stands as a testament to sustainable water management, innovative construction, and environmental stewardship, promising water security and ecological conservation for future generations.
HEAVY CIVIL $150 MILLION TO $250 MILLION
Balfour Beatty – Sterling Natural Resource Center (SNRC)
The Sterling Natural Resource Center (SNRC) SNRC’s transformation includes a $33 million biosolids processing upgrade, incorporating two massive digester tanks, enhancing both functionality and efficiency. Despite these additions and the global pandemic, the project maintained its schedule with only a modest six-month extension. Through Technical Working Groups, the project fast-tracked timelines, reducing additional bidding phases and optimizing equipment selections.
Sustainability is a cornerstone of SNRC, producing renewable electricity equivalent to powering approximately 1,950 homes, and offers a vital renewable water supply for 600,000 residents. The facility efficiently utilizes land with its Membrane Bioreactor technology, maximizing its 20-acre site with community spaces, gardens, and recreational areas.
SNRC serves as a beacon of community pride in a disadvantaged area, enhancing local aesthetics and providing educational pathways in environmental science. Team Sterling’s commitment to inclusivity and safety resulted in an exemplary safety record and engaged community stakeholders through innovative outreach and education programs.
Myers-Rados, JV – I-15/SR 91 Express Lane Connector Design-Build
The SR 91 corridor project is a transformative infrastructure initiative aimed at enhancing connectivity and reducing traffic congestion in one of the region’s busiest corridors. This project completes a crucial link between two tolled facilities by adding 32 bridge spans and 8 lane miles of pavement, facilitating smoother access to the SR 91 corridor for Eastvale, Jurupa Valley, Corona, and Norco residents. Key features include a 1,700-foot Express Lane flyover, multiple bridges, and robust pavement enhancements to improve travel time reliability and safety.
The Myers-Rados joint venture, alongside T.Y. Lin International collaborative efforts led to $25 million in cost savings and accelerated construction by six months. The project tackled unique challenges such as narrow work zones, complex staging sequences, and coordination with multiple stakeholders, including Caltrans and local agencies, to minimize disruptions.
Flatiron – Route 210 Roadway Rehabilitation
The Route 210 Roadway Rehabilitation and Lane Replacements Project is a pivotal infrastructure initiative extending over 52 lane miles from Wheatland Avenue to Interstate 5 in Sylmar, California. This project, funded by SB 1, aimed to revitalize heavily trafficked pavement, ramps, connectors, and safety systems while enhancing freeway lighting, traffic signals, and ADA compliance. A focus on sustainability included installing stormwater treatment devices like Biofiltration Swales and Bioswales.
The project faced challenges such as a concrete shortage and COVID-19 impacts, which were mitigated through proactive management and innovative solutions, including using alternative suppliers and efficient traffic management.
Innovative solutions included polyester concrete overlays for bridge decks, reducing long-term maintenance costs and enhancing safety. Sustainability was further promoted by on-site batching of Portland Cement Concrete Pavement (PCCP), minimizing environmental impact. The project also successfully incorporated recycled pavement through a partnership with FHWA, setting a U.S. milestone.
BUILDER $20 MILLION & UNDER
Clark Construction Group – SeaWorld Arctic Rescue Roller Coaster
SeaWorld San Diego’s Arctic Rescue roller coaster project involved tackling significant engineering challenges. The project faced complex utility systems and strict safety requirements near a marine habitat. A critical task was decommissioning an old ride while preserving essential utilities, including a 12,000-volt duct bank. Clark Construction addressed this by installing horizontal micropiles under the duct bank to prevent disruption and support the foundation. When unsuitable soil was found, it was replaced with rock to ensure stability, with column piers adjusted accordingly.
To meet seismic standards, a continuous mat foundation was installed, converting metric designs to imperial measurements for accuracy. 3D building information modeling (BIM) was utilized to coordinate structural elements, facilitating the ride’s assembly. Delays from the California Coastal Commission were managed by re-sequencing tasks and leveraging industry connections to expedite the schedule.
With incomplete structural designs, Clark Construction adapted the construction sequence, starting from the site perimeter inward. Despite labor and concrete shortages, the team maintained progress by selecting reliable contractors. The project scope expanded to include thematic elements like Arctic-inspired decorations, LED ceilings, murals, and props, such as a decommissioned helicopter.
Throughout, Clark Construction prioritized animal safety, implementing dust control and working closely with the park’s veterinary team near sensitive beluga exhibits. This project highlights the company’s innovative approach to solving engineering challenges and managing construction effectively.
Otto Construction – Fairytale Town Story Center and Welcome Center
The 2,782-square-foot Story Center introduces Fairytale Town’s first indoor program space, featuring a children’s play area, a reading nook, and an outdoor amphitheater for creative activities and educational workshops. Meanwhile, the 2,956-square-foot Welcome Center offers essential office space, a new box office, a gift shop, and accessible restrooms, all crucial for managing the park’s growing visitor numbers.
The construction process demanded exceptional craftsmanship, with the Story Center’s roof requiring hand-cut framing to achieve its storybook aesthetic. Unique features like custom-built dormers and a synthetic thatch roof enhance the fairytale ambiance. Otto Construction’s team executed onsite carpentry, employing traditional methods that taught and honed their skills. Safety was paramount as Fairytale Town is surrounded by busy community facilities. Otto Construction maintained rigorous safety standards, resulting in zero incidents during construction.
Community involvement played a significant role, with generous donations enabling the project despite budget constraints. Value engineering solutions, like plaster shaped to look like stone, helped preserve the park’s charm within budget limits.
Swinerton – Air Canada SFO Maple Leaf Lounge
The Maple Leaf Lounge at San Francisco International Airport (SFO) Terminal 2 exemplifies Air Canada’s commitment to luxury and innovation. Designed by Gensler and constructed by Swinerton Builders, this 165-seat lounge spans 8,168 square feet and features an array of amenities, including biometric e-gates, multiple lounge areas, a buffet, a full bar, and an outdoor terrace with fireplaces. Guests can relax in leather armchairs with USB outlets, enjoy the artwork, and utilize private workrooms, shower rooms, and a VIP section.
The lounge’s design includes high-end finishes such as NanaWalls and custom millwork, complemented by vibrant murals and stonework that reflect the partnership between Air Canada and SFO. Despite the complexities of working in an active airport, the project was completed on time and 5.76% under budget. Challenges such as limited access and supply chain constraints were addressed through strategic planning and collaboration with stakeholders.
Swinerton’s team overcame obstacles like overhead ceiling congestion by utilizing an Armstrong Gypsum Board System, ensuring a seamless integration of mechanical, electrical, and plumbing elements. The flooring required precise preparation to transition smoothly between different materials. During one of the wettest winters, waterproofing was rigorously tested to maintain quality.
Safety was paramount, with a tailored safety plan developed to protect the project team and airport operations. The successful execution of the Maple Leaf Lounge underscores the project’s excellence in design, construction, and project management, setting a new standard for airport lounges.
BUILDER $20 MILLION & $100 MILLION
Bogard Construction – Live Oak Health & Housing Campus
The Live Oak Health & Housing Campus in Santa Cruz County is a significant construction project addressing critical community needs for housing and healthcare. The $51 million development involves six buildings, four prime contracts, and three clients, including MidPen Housing, Dientes Community Dental, and Santa Cruz Community Health. The project was designed to transform 3.7 acres of underutilized land into a mixed-use space, providing integrated services in a community where healthcare and housing shortages are prevalent.
The campus features a 20,126 sq. ft. medical clinic and a 5,790 sq. ft. dental clinic, serving 10,000 medical and 6,000 dental patients annually. The Bienestar Plaza, a four-building residential complex, offers 57 units for individuals and families earning 30% to 80% of the area median income. Amenities include a community courtyard, playground, and various resident services. The project collaborates with the County’s Health Services Agency to provide housing and case management for those experiencing homelessness, aiming to improve health outcomes and reduce emergency service usage.
Challenges such as the pandemic, site mediation, design changes, and material cost escalations were managed, keeping the project within $100,000 of the budget and six months of the timeline.
Hensel Phelps – University of California, Riverside School of Medicine Education Building II
Designed to support the medically underserved Riverside County region, the School of Medicine (SOM) Education Building II (EDII) at UCR is a 90,000 GSF, five-story structure aimed at training a diverse workforce of physicians. The building consolidates student learning spaces, faculty offices, and social areas, enhancing the SOM’s presence on campus. Strategically located, the EDII maximizes its lifespan through a flexible design adaptable to future growth. The layout places high-activity learning spaces on the first three floors and administrative functions above. Outdoor environments on each level promote collaboration and reflection.
The building anchors the eastern edge of the campus within the SOM Precinct, connecting existing and future buildings into a cohesive environment. The design utilizes the constrained site effectively, creating internal and external connections and providing multiple accessible entry points. Features include a large Level 2 terrace and balconies, with a main entry that integrates indoor and outdoor spaces. Learning studios on Level 1 offer over 7,000 SF of flexible space with advanced projection technologies and acoustics.
Swinerton – 4930 Directors Place
4930 Director’s Place is a cutting-edge, five-story life sciences research and office building spanning 397,776 square feet. Designed with sustainability at its core, the building is targeting LEED Silver certification, featuring low-VOC materials and an energy-efficient smart glazing system. The project emphasizes natural light through a narrow floor plate and electrochromic smart windows, reducing heat gain and enhancing occupant comfort. Water and energy-efficient systems are integrated throughout the campus, supporting its sustainability goals.
Swinerton played a pivotal role in construction, particularly in concrete, metal framing, and other key areas, ensuring the project was completed efficiently. The facility includes a beautiful central event lawn with art installations, encouraging community engagement. The three levels of underground parking provide green vehicle spaces and electric charging stations, promoting eco-friendly commuting.
Innovative construction techniques, such as simultaneous steel frame and parking garage construction, significantly reduced the project timeline. Despite challenges like site constraints and additional building requests, Swinerton and Delawie delivered a high-quality product on time and within budget. The building’s smart glass façade not only enhances aesthetic appeal but also optimizes natural light, promoting healthier, more productive environments.
Turner Construction Company – Placer County Health & Human Services Center
The New Placer County Health & Human Services Center is a groundbreaking 149,000 square foot facility, designed as the county’s first zero net-energy building. This two-story steel-framed structure integrates sustainable features like carport-mounted photovoltaic panels, energy-efficient systems, and water-saving measures, aiming for minimal environmental impact. Its design fosters collaboration by consolidating six service divisions under one roof, enhancing access to essential services for residents, especially vulnerable populations.
The site plan promotes community well-being with a central lobby, “Collaboration Street” for team integration, and outdoor spaces inspired by a river theme, symbolizing the journey from illness to health. The facility includes amenities like children’s play areas and outdoor patios, creating a welcoming atmosphere.
BUILDER $100 MILLION & $200 MILLION
Stronghold Engineering, Inc. – Heating, Ventilation, and Air Conditioning System at Ironwood State Prison
Stronghold Engineering was contracted by the California Department of Corrections and Rehabilitation (CDCR) for a large-scale retrofit project at Ironwood State Prison, covering 350 acres and over 1 million square feet. The project scope included constructing a new Central Chilled Water Plant, achieving LEED Silver certification, and installing a chilled water loop for 99 buildings with 244 new Air Handling Units. Additionally, a new medium voltage switchgear was set up for dedicated power, along with new fire alarm systems and Zero Net Energy (ZNE) meters. Roofing work included new PVC roofs and cool roof coatings. A significant addition was a 1.2-million-gallon chilled water storage tank.
Stronghold self-performed 43% of the labor, handling tasks like electrical work, concrete, and fireproofing. The project faced challenges due to COVID-19, requiring work schedule adjustments and logistical complexities in an occupied prison environment. Entry and exit procedures, tool inventory, and strict safety protocols, including heat illness prevention, were crucial. The project included 46 subcontractors and 134 vendors covering various specialties. Delays were managed by revising schedules, and Stronghold assisted with deferred maintenance to expedite fire alarm permits from the California State Fire Marshal.
Swinerton – Behring Pavilion: Home of the UCSF – John Muir Health Jean and Ken Hofmann Cancer Center
The Behring Pavilion, home to the UCSF – John Muir Health Jean and Ken Hofmann Cancer Center in Walnut Creek, CA, is a 155,000-square-foot outpatient facility designed by SmithGroup. It supports advanced cancer care with imaging services, radiation oncology, and infusion departments, among others. The project involved demolishing existing buildings, relocating utilities, upgrading a central utility plant, and constructing a solar-powered parking lot.
Led by Swinerton, the construction overcame several challenges, such as adhering to building height requirements through strategic site design and implementing a complex power system that included a new solar installation and emergency power upgrades. The proactive quality control program ensured precise construction, particularly for the heavily reinforced concrete vaults housing the linear accelerators. A significant challenge arose when a water valve break flooded the facility, requiring rapid remediation to maintain the construction schedule.
COMMUNITY SERVICE
Swinerton – Kaiser Permanente Watts Medical Offices & Watts Counseling, and Learning Center
The Kaiser Permanente Watts Medical Offices & Watts Counseling and Learning Center is a comprehensive facility in South Los Angeles, offering medical, counseling, and educational services. Spanning 61,900 square feet with an additional 105,713-square-foot parking structure, the center is designed to achieve LEED Silver status. Its East wing includes a preschool and community kitchen, while the West wing houses medical services, a pharmacy, and behavioral health facilities. The project features innovative design elements, such as a fruit-themed mosaic and a ceramic tile mural honoring the Watts Towers.
The project team employed innovative solutions to overcome challenges, such as using ConXtech structural steel to expedite construction. They also managed utility limitations by collaborating with providers to enhance electrical capacity for both the project and the community. Unforeseen issues like water seepage during garage excavation were swiftly addressed, ensuring the project remained on schedule and within budget.
Yerba Buena Engineering & Construction, Inc. – SOMA Street Tree Nursery Site Improvements
Yerba Buena Engineering & Construction, Inc. collaborated with San Francisco Public Works (SFPW) and Caltrans to transform a former homeless encampment into a vibrant nursery for urban forestry. Located between two downtown freeway ramps, this project aims to increase San Francisco’s urban tree canopy, particularly in underserved neighborhoods, by cultivating tree species adapted to the city’s diverse microclimates. In addition to greening the city, the nursery supports a workforce development program, training disadvantaged individuals in urban forestry, and serves as an educational hub promoting environmental sustainability.
The project includes two modular buildings made from shipping containers, housing classrooms, offices, and restrooms. Powered by a photovoltaic system, the site operates independently from the electric grid, featuring solar panels and energy storage for resilience. Sustainable practices extend to irrigation, organic soil use, and waste management, reflecting a strong commitment to environmental stewardship.
This project not only enhances green spaces and air quality but also addresses environmental justice by providing recreational and aesthetic benefits to historically neglected communities. It stands as a model for how construction projects can deliver significant social and environmental benefits, embodying San Francisco’s vision for sustainable urban development.
EXCELLENCE IN PARTNERING
Balfour Beatty – Sterling Natural Resource Center (SNRC)
Situated in an urban setting, the Sterling Natural Resource Center (SNRC) is an innovative wastewater treatment facility dedicated to “Make Every Source a Resource.” It employs advanced technologies like Membrane Bioreactor (MBR) and Ultraviolet (UV) disinfection, enabling the recycling of up to eight million gallons per day to support water sustainability and combat drought. Designed for community benefit, SNRC includes odor control systems and offers educational programs to promote environmental awareness. Its compact design integrates treatment steps, eliminating large settling tanks and ensuring pathogen-free water without chemical residues.
During the COVID-19 pandemic, SNRC faced supply chain disruptions, leading to the strategic use of stainless steel instead of ductile iron pipe, improving infrastructure quality. This decision showcases the team’s agility and risk management in maintaining project timelines and maximizing long-term benefits. Sustainability is further enhanced by on-site renewable energy generation through co-digestion, producing enough electricity to power nearly 1,950 homes, thus reducing carbon emissions and operational costs. The facility’s landscape supports water efficiency and carbon sequestration with features like a picnic area and demonstration garden. SNRC sets a benchmark in sustainable infrastructure, highlighting the impact of innovative design and collaborative planning on long-term environmental and community gains.
Teichert Construction – Veterans Boulevard Interchange
Fresno’s Veterans Boulevard Interchange Project is a landmark infrastructure development first envisioned in the city’s 1984 General Plan. Enhancing traffic flow and accessibility to SR-99, the project includes a distinctive grade-separated trail for pedestrians and cyclists, improving safety and connectivity in previously isolated areas. This massive public works endeavor, realized by Teichert and MCM, introduced a six-lane super-arterial road, new freeway interchange, bridges, ramps, and a pedestrian trail, marking it as Fresno’s largest infrastructure project.
Teichert’s project management was exemplary, coordinating multiple stakeholders like Caltrans and the City of Fresno, while integrating ongoing projects such as the High-Speed Rail. Strategic initiatives, including value engineering, allowed the inclusion of $1 million in additional project scope while staying within budget. Innovations in traffic rerouting minimized disruptions and cut 20 days from the schedule, saving $250,000. The emphasis on safety yielded zero OSHA incidents, exemplifying efficient and secure project execution.
Collaborative efforts and strategic problem-solving addressed unexpected challenges, such as soil conditions, saving $430,000 and preventing delays. Recycling excavated materials further reduced environmental impacts and costs. Concluding on time and under budget, the project significantly enhances Fresno’s transportation infrastructure, fulfilling a vision nearly four decades in the making.
Manson Construction, Co. – P-443 Pier 6 Replacement at Naval Base San Diego
P-443 Pier 6 Replacement at Naval Base San Diego marked a successful collaboration between NAVFAC Southwest and Manson Construction Co., mirroring previous achievements at the base. Designed to replace an aging 1945 pier, the project introduced a modern 1,500 ft by 120 ft pier, accommodating four naval vessels. This new structure features 516 prestressed concrete piles and over 17,000 cubic yards of cast-in-place concrete, ensuring resilience and utility for modern naval operations. Enhancements include updated mechanical and electrical utilities, guard facilities, lighting, and other essential appurtenances, designed for a 75-year service life following UFC 4-152-01 standards.
The project’s innovation was underscored by concurrent demolition and reconstruction, facilitated by a partnership with WSP USA. This approach, combined with detailed planning, allowed the project to complete one month ahead of an aggressive schedule. Collaboration between contractor and client minimized operational disruptions and led to no major rework or claims. The effort garnered exceptional ratings in quality, schedule, cost control, management, and regulatory compliance in CPAR evaluations.
MEGAPROJECTS
Hensel Phelps – Delta Sky Way Program at Los Angeles International Airport
The Delta Sky Way Program at Los Angeles International Airport (LAX) is a major infrastructure project that relocated Delta Air Lines from Terminals 5 and 6 to Terminals 2 and 3 to support growing operations and enhance the guest experience. The project involved creating a new 27-gate facility by consolidating Terminals 2 and 3, featuring enlarged concourses, automated security lanes, and modern amenities. It established direct connections to the Tom Bradley International Terminal via a secure airside connector, improving passenger flow without re-entering security checkpoints. The redevelopment increased capacity, enhanced baggage handling, and optimized airline operations.
Advanced construction techniques were employed, such as Building Information Modeling (BIM) and Virtual Design and Construction (VDC), to improve coordination and project management. The seismic system used innovative bolted SidePlate connections, expediting structural steel erection and subsequent trades. High-performance materials and innovative glazing solutions boosted structural integrity and energy efficiency. The project also included modernized wayfinding, amenities, and advanced security systems.
The project scope expanded due to client-initiated changes, requiring additional resources and adjustments, which increased the contract cost. The Delta Sky Way Program received several awards, including the 2024 ENR California Regional Best Project Award for Airport/Transit.
California Rail Builders – High Speed Rail- Construction Package 4
California Rail Builders (CRB), a joint venture between Ferrovial Construction and Griffith Company, served as the design-build contractor for Construction Package 4 (CP 4) of the California High Speed Rail project. This package included the construction of a 22-mile stretch of rail and 11 civil structures such as overpasses, underpasses, and viaducts. The project spans from north of the Tulare-Kern County line to Poplar Avenue in Kern County. Construction commenced in late 2017 and reached substantial completion in January 2024, making it the first construction package to achieve this milestone.
Safety enhancements were a priority, including the removal of five BNSF crossings, benefiting the Wasco community. Key structures include the McCombs and Merced Grade Separations and the Poso Avenue underpass, designed for both vehicular and pedestrian traffic. The Wasco Viaduct, the largest structure in this project, spans 1,995 feet.
CP 4 generated over 3,000 jobs and involved over 90 small businesses, infusing $169 million into subcontract agreements. CRB’s collaboration with the City of Wasco led to significant local infrastructure improvements, including a new well and sewer lines. CRB’s commitment to community relations was evident through outreach and support for local events, emphasizing the importance of teamwork in achieving project goals.
Mortenson – Edwards and Sanborn Solar and Energy Storage Project
The Edwards and Sanborn Solar and Energy Storage Project, located in Kern County, California, is a monumental renewable energy initiative and the largest of its kind in the United States. Spanning 4,600 acres, it boasts 864 megawatts of solar power and 3,287 megawatt-hours of energy storage, powering over 500,000 homes in the CAISO grid. This project, situated on Edwards Air Force Base, leverages an enhanced use lease program, marking it as the largest project in U.S. Air Force history and significantly reducing carbon emissions in line with California’s climate goals.
Despite its scale, the project only faced one environmental citation related to dust emissions, which was promptly resolved, underscoring its commitment to minimizing environmental impact. Economically, it fueled regional growth by employing over 860 local craftworkers, achieving over a million injury-free work hours.